7.ライン総合効率の改善 総合効率阻害要因の調査
7-2.総合効率阻害要因の調査
改善対象ラインが人主体のラインなら『ライン総合効率』、また機械主体なら『ライン設備総合効率』の現状値が判ったら、何故100%を大きく下回るのか、その要因が何なのかを特定するための調査に入ります。
稼働分析の手法としてIE書に載っている「連続観測法」、「ワークサンプリング法」と私が実践している「ビデオ観測法」を説明します。
何れの方法で調査しても、繰返し作業から外れた「非繰返し作業」を見付けることがこの調査の主目的で、これさえ見つかれば『総合効率』の飛躍的な改善は可能です。
7-2-1.連続観測法
1)連続観測法の特徴
- 対象とする人又は機械について、観測者が一対一対応で始業時から終業時まで連続して観測し、発生した事象を細大漏らさず記録します。
- この方法は最も労力を要しますが、きめ細かい問題点の抽出が可能です。
- 反面、この時計を見ながらの観測法は、余程手馴れた人でないと記録遅れが出たり、また観測で得られた情報を他の人と共有するのが難しい。
- 対策案を作成するとき、調査記録不足で再調査が必要となることがある。
※従って、後述の「ビデオ観測法」 をお勧めしたい。
2)連続観測法による調査の進め方
- 原則として始業時から終業時まで、対象ラインの勤務時間に合わせて観測します。
- 観測板に『非繰返し作業調査表』(F-06)とデジタル時計を見易い場所に固定し、調査対象(人又は機械)、時計、「非繰返し作業調査表」を同一視線上に置きます。
- 観測者は対象の人又は機械が良く見えて、作業の邪魔にならない場所に立ちます。

- 非繰返し作業は、その発生時刻、終了時刻と非繰返し作業の内容を記録します。
時刻は時:分を記入します。
- 非繰返し作業による正味停止時間の記入は観察の合間や調査完了後に行います。
- 時計はストップウォッチではなくデジタル時計を使い、非繰返し作業が何時ごろ発生したかが判るようにします。
- 対策案は「その非繰返し作業を排除または極小化する」ことを前提に皆で知恵を出し合って作成します。おおよその効果時間を査定します。
- 出来あがった対策案の効果時間を集計し、当初予定した総合効率が達成できるか確認する。例えば効果時間が30分なら、
▲30分 ÷ 480分 = ▲6.3%
- 達成不可であれば更なる改善を行う。
- 対策案は誰が何時までに完了するかの予定を決めて、改善活動に入る。
『非繰返し作業調査表』(F-06)は、GIF形式でダウンロードできますので、ご活用ください。
7-2-2.ワークサンプリング法
1)ワークサンプリング法(瞬間観測法)の特徴
- 確率の法則を活用して、観測者がランダムに定めた時間に瞬間観測を行い稼働状況を把握する方法で、1人で何人もの人や機械を観測できますが、深く追求するには不適で、再調査が必要となります。
- 長所は、観測とその後のデータの整理が容易で、1人で何人もの人や機械の状況が観測でき、また作業者が余り意識しなくて済むので、実態に近い数値が得られることです。
- 短所は、瞬間的な観測なので深い研究には不向きで、また職場を離席した場合の行動が判らなかったり、サンブル数が少ないと誤差が大きいことがあるので、観測数が多くなり観測時間が掛かります。
<目的> <必要観測回数>
(1)問題の所在確認など 100
(2)手待ちなどの原因分析 600
(3)段取りや遅れの比率調査 2000
(4)人又は機械の稼働率調査 4000
- 総合効率阻害項目は判るが、対策案を作成するとき再調査が必要となる。
※従って、後述の「ビデオ観測法」 をお勧めしたい。
2)ワークサンプリングの進め方
ワークサンプリングに付いては色々なIE書で詳しく説明されているので、難しい理論についての説明は割愛します。ここでは実務面の説明をします。
- 観測内容の明確化を図る
内容としては、繰返し作業を阻害する『総合効率低下の10項目』がそれぞれどのくらい発生しているのかがわかるように項目を決める。
- 現場の責任者や作業者に協力要請する
責任者から作業者に趣旨説明する。また通常通りの作業をするようにお願いする。
- 観測数:Nを決める。

N : 必要な観測数
α : 結果の信頼度95%とすると α=1.96
S : 相対誤差 = ±5%(仮定)
P : 推定稼働率 … 予備観測で求めるか対象ラインの基準時間と工数原単位が判れば、式Aから求める。
注1)一般に観測数Nを決めるときは、特に理由の無い限り信頼度95%とする場合が多い。
注2)推定稼働率の求め方 … 例、或る工作機械5台の稼働状況は、予備観測で25回巡回し、稼働していたのが延べ100回だったとき、推定稼働率Pは
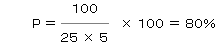
として求めます。
注3)また対象ラインの総基準時間と工数原単位が判って入れば、式Aより求める。
P ≒ ライン総合効率 = 総基準時間 ÷ 工数原単位
よって式Hは下のようになる。

例えば、P=70%なら

- 1日の巡回回数を決める。
平均何分間隔で回れるかを考えて決める。
例えば20分なら 480分 ÷ 20分 = 24回/日 となり、必要日数は 686回 ÷ 24回/日 ≒ 30日 となります。
実際問題として、これが難しいときは回数を見なおしてください。
(ワークサンプリングをすることが目的ではないので)
- 観測時刻をランダム時刻表により決める。

- 巡回経路は予め決めておく。
- 観測結果は『ワークサンプリング観測用紙』(F-08)に記録する。
- 観測結果を集計し、比率の高い項目から対策する。
『ランダム時刻表』(F-07)は、GIF形式で、『ワークサンプリング観測用紙』(F-08)も、GIF形式で、ダウンロードできますので、ご活用ください。
7-2-3.ビデオ観測法
1)ビデオ観測法(連続観測法)の特徴
- 対象とするライン(数人)または数台の機械について、始業時から終業時までの非繰返し作業の観測が1人で対応できる。
- 「連続観測法」や「ワークサンプリング法」での目視での観測では得られない多量の記録をすることができる。
- ビデオ分析では観測者以外の人も問題点の抽出や改善策作りに容易に参画でき、またその時の状況が何時でも再現することができる。
- また機械のチョコ停調査ではビデオカメラを固定して無人撮影し、その後のビデオ分析では微細送りにより原因究明がやりやすい。
- 観測記録の再現で対策案が作成でき、再調査が殆ど不要となる。
2)ビデオ観測法による調査の進め方
- 前述の「連続観測法」と同様、原則として始業時から終業時までビデオ撮りします。
- 連続2,3時間ビデオ撮りが出来るようなビデオカメラを準備します。ビデオの撮り方は 6-2-3.ビデオによる現場観察を参照して下さい。
- 調査対象ラインが2~3名、設備で2~3台なら、1台のビデオで対応出来ます。
- 三脚を使用してのビデオ撮りは極力避け、肉眼で見ながら撮影します。ビデオ画面だけでは判断しにくいことがありますし、人の場合ではビデオ画面からその人が消え、どうしてラインを離れたかが判らなくなります。
- 設備のチョコ停調査では三脚での固定撮影でも良いと思います。
- ビデオ撮りが終わったら、ビデオを見ながら『非繰返し作業調査表』(F-06)に非繰返し作業を記入します。
- 正規の繰返し作業は倍速送りまたは早送りし、また問題の個所は微細送り(1/30秒)で調査します。
- その他は上記の「連続観測法」と同様です。
- 『非繰返し作業調査表』(F-06)を集計し、問題の大きい項目から改善策を作成し、対策する。
※非繰返し作業の調査は筆者の経験より、ビデオ観測法を推奨したい。
7-2-4.予想される阻害要因対策
ラインの総合効率を阻害する要因の絞込みが出来たら対策に入るわけですが、いずれも簡単につぶせるものでは有りません。阻害要因の絞込みができれば、見通しは明るいと思います。一つ一つ根気強く対応するしか方法は無いと思いす。製造、技術部門が一体となって、総力をあげて取り組むことが必要です。
1)始業時の立上りロス対策
例えば或るラインで、始業が8時で最初の良品が8時20分に出てくるとき、何故20分のロスタイムが発生するのか、始業時から現場観察し、その要因を列挙し根気強くつぶして行けば立上りロスは大幅に削減できるはずです。
2)チョコ停対策
チョコ停発生個所のビデオ撮りを行い、チョコ停発生のメカニズムを見つけだし対策する。ビデオの微細送り(1/30秒)で究明してみるのもよい。
3)刃具交換,調整対策
刃具は機外でプリセットして、機械に取付けたら調整しないで使えるようにする。調整レスの刃具交換とするために、加工精度に合ったプリセットゲージを使用するなどの見直しをする。
4)品質不良、手直し対策
不良・手直しの発生メカニズムを明確にし、対策する。必要ならポカヨケや人手を掛けない、ローコストな全数検査を取り入れる。
5)終業時の後始末対策
立上りロス対策同様、現場観察を行い、その原因を取り除く。
6)材料、部品待ち対策
特に組立ラインでは、組立部品が全部揃わないための作業待ちやラインの組換えにより、ラインの総合効率が低下しているのを良く見かけますが、組立ラインの改善では先ずこの遅れ部品の対策を行うことが重要です。
7)作業者による部品運搬
加工、組立ラインの作業者が材料、部品、完成品の運搬を行っているのを見かけますが、総合効率の面から、監督者や水すましが運搬、供給業務を行うようにする。その際、表示灯による呼出しなどを活用する。
8)ラインバランス不良による手待ち対策
数人の加工、組立ラインでは、作業配分が悪いために手待ちが発生していることがあります。作業配分表やマン・マシンチャートを作成して、手待ちの無いことを確認します。
講座トップ
ページ上部へ戻る